Фрезерування — дуже розповсюджений вид обробки металів різанням: у машинобудуванні фрезерування складає біля 15 % всіх видів обробки різанням. Фрезеруванням можна оброблювати площини, уступи, пази, канавки, фасонні поверхні, зубчасті колеса, різь, різати Для фрезерування застосовують фрезерні верстати. Інструментом для фрезерування є фрези — багатолезовий інструмент, кожен зуб якого являє собою різець. У фрезеруванні беруть участь водночас декілька зуб’їв, останні з яких під час роботи встигають трохи охолонути. Таким чином, процес різання при фрезеруванні відрізняється від безперервного різання при точінні та свердлінні тим, що зуб'я фрези працюють періодично. Це підвищує стійкість інструмента і забезпечує високу продуктивність обробки.
Останнє сприяло великому поширенню фрезерування в металообробній промисловості, бо цей процес обробки досить універсальний. Він забезпечує високу точність обробки виробів до восьмого — дев'ятого квалітетів і шорсткість четвертого-сьомого класів.
Фрезеруванням можна оброблювати різноманітні плоскі, фасонні та гвинтові поверхні, виконувати, наприклад, такі роботи, як виготовлення зуб’їв зубчастих коліс, розверток, зенкерів, нарізування шліцьових пазів на валах, шпонкових канавок різних багатогранників тощо. Найпоширенішими вадами фрезерування з застосуванням різних фрезерних інструментів є обробка площин горизонтальних і похилих скосів, уступів, пазів, різних гвинтових канавок і фасонних поверхонь, зубчастих коліс, рейок і секторів, а також розрізування та відрізування заготовок.
Багатолезовий фрезерний інструмент — фреза має на циліндричній поверхні зуб’я, які нагадують набір кількох різців.
Зуб’я можуть розміщуватися не лише на циліндричній поверхні, а й на торці фрези. Тому залежно від розміщення зуб’їв на поверхні фрези їх називають циліндричними та торцевими.
Фрезеруваня поских поверхностей
|
Для фрезерування треба обертати фрези навколо своєї осі, а заготовку або фрезу поступально переміщувати. Ці два рухи сприяють зрізуванню зуб’їв фрези в поверхню заготовки, а при переміщенні її знімають з
!неї стружку. Обертальний рух фреза одержує завдяки обертанню шпинделя верстата, а шпинделю обертання надає електродвигун верстата. Поступальний рух поздовжній, поперечний і вертикальний при фрезеруванні надає механізм подачі верстата. Два рухи фрезерування: головний рух обертання фрези і рух подачі — поступальне переміщення,.показано на рис. 2.1.У процесі різання при фрезеруванні швидкість головного руху за величиною більша швидкості руху подачі.
При фрезеруванні процес різання супроводжується утворенням стружки із шару металу, що зрізується різальним інструментом. Залежно від
умов обробки металу та інших факторів стружка (шар зрізаного металу) може мати різний вигляд процес утворення стружки при фрезеруванні зуб’ями фрези — це наслідок зсування частинок металу однієї відносно інших з відокремленням від загальної маси у вигляді стружки. Зуб’я — це ті різці, які встановлені на циліндрі або торці (рис. 2.2) для циліндричного і торцевого фрезерування.

Рис. 2.1. Головний рух і рух подачі

РИС. 2.2. Схема процесу фрезерування:
а — циліндричного; б — торцевого: — оброблювана поверхня; 2 — оброблена поверхня; 3 -поверхня різання
Геометрія різальної частини різця (зуба фрези), його поверхні і кути показані на рис. 2.3. Оброблюваною називається поверхня, яку треба обробити, а обробленою — поверхня, з якої вже знято стружку.Поверхнею різання називається поверхня від обробленої до оброблюваної, утворена головною різальною кромкою різця (зуба фрези). Передньою поверхнею називається поверхня, по якій сходить стружка. Задньою поверхнею називається поверхня, яка повернута до оброблюваного виробу.

Рис. 2.3. Площина різання та кути зуба фрези
Поняття про поверхню різання можна сформулювати так:
поверхня різання — це поверхня, що утворюється на оброблюваній деталі безпосередньо різальним лезом інструмента і є перехідною між оброблюваною і обробленою поверхнями. Таке визначення поняття про поверхню різання полегшує визначення поняття про площину різання, бо вона уявна площина, яку ми будуємо, уявляючи, що вона дотична до поверхні різання в даній точці.
Площиною різання називають площину, що проходить по дотичній до кола, утвореного вершинами зуб’їв фрези, і (завжди) через головну різальну кромку (див. рис. 2.3). Різальна кромка утворюється перетином передньої та задньої поверхонь й виконує роботу різання.
Передній кут γ — кут між передньою поверхнею і площиною, перпендикулярною площині різання, яка проходить через різальну кромку.
Кут загострення β — кут між передньою та задньою поверхнями.
Задній кут α — кут між дотичною до задньої поверхні в даній точці різальної кромки і площиною різання. Сума кутів α, β і γ завжди 90º, тобто
α + β + γ = 90°. (2.1)
Кут між передньою площиною і площиною різання називають кутом різання та позначають 8. Між кутами а, р, у і 8 існує така залежність:
δ = α + β = 90° - γ. (2.2)
При обробці різанням різальна кромка інструмента залежно від напряму руху характеризується кутом нахилу λ.
Кутом нахилу λ називають кут між різальною кромкою і перпендикуляром до напряму руху інструмента.Розрізнюють також кути в плані: головний кут у плані φ, допоміжнийкут у плані φ1, та кут при вершині в плані ε.
Головним кутом у плані називають кут, який утворюється між проекцією головної різальної кромки та напрямом подачі.
Допоміжним кутом у плані називають кут між допоміжною різальною кромкою і напрямом подачі.
Кутом при вершині у плані називають кут, який утворюється перетином головної та допоміжної різальних кромок.
Елементи режиму різання при фрезеруванні
Процес обробки металів фрезеруванням здійснюють на фрезерних верстатах багатолезовим різальним інструментом — фрезою. Геометрія різальної частини фрезерного інструмента подібна до різця, але фрезерування має і свої особливості, наприклад, це змінність стружки, яку знімаємою за товщиною. В процесі фрезерування бере участь не один різець, а декілька зуб’їв фрези, кожне різальне лезо (зуб) фрези працює з перервами. Різальним інструментом можна також працювати за двома схемами різання: проти подачі та в напрямі подачі.Таким чином, при фрезеруванні за першою схемою зуб фрез знімає незначної товщини стружку, а при фрезеруванні за друго схемою, навпаки, спочатку знімається найтовща стружка.Колове розміщення зуб’їв фрези полегшує умови роботи, бо вони обертаються з переривами. Залежно від дуги контакту одночасно може працювати не один зуб фрези, а декілька.
Режим різання при фрезеруванні різними фрезерними інструментами характеризується глибиною й шириною фрезерування швидкістю різання і подачею.
На всіх заготовках, які обробляються фрезеруванням, розрізнюють глибину фрезерування t (глибина різання) і ширину фрезерування В.
Глибина фрезерування — це товщина шару металу, що зрізується за один прохід фрезою (рис. 2.4), або відстань між оброблюваною і обробленою поверхнями, виміряна перпендикулярно до обробленої поверхні. Величину глибини фрезерування вибирають залежно від-кількох факторів — величини припуску на обробку, класу шорсткості ті поверхні виробу та можливості фрезерного верстата і фрези.

Рис. 2.4. Глибина різання фрезами:
а — торцевою; б — кінцевою; в — дисковою
Обробляють заготовку за один прохід, якщо припуск можна зняти за один прохід. Шорсткість поверхні незначна, якщо потужність верстата та різальний інструмент дають змогу зняти стружку за один прохід. Якщо вимоги до поверхні, що фрезерується, підвищені, припуск знімають за кілька проходів. Найчастіше при чорновому фрезеруванні призначають глибину різання 4...5 мм, але вона може бути й 20...25 мм при застосуванні потужних верстатів і торцевих фрез з твердосплавними пластинками. Для чистового фрезерування призначають глибину різання 1...2 мм.
Ширина фрезерування — це ширина обробленої за один прохід поверхні заготовки. У випадках, коли заготовку фрезерують набором фрез, то ширина фрезерування визначається як сума ширини всіх поверхонь з'єднаних фрез.
Швидкість різання у — це довжина шляху (в метрах), який проходить за одну хвилину найбільш віддалена відносно осі обертання точка головної різальної кромки зуба фрези.
Частота обертання шпинделя верстата п завжди відома, тому швидкість різання може бути визначеною. Відомо, що за один оберт фрези різальне лезо зуба фрези діаметром О пройде шлях, що дорівнює довжині кола, тобто І = πD мммм. Для визначення шляху, пройденого лезом зуба фрези за кілька обертів, треба помножити довжину шляху за один оберт на число обертів п, тоді
L = ln = πD n мм/хв,
а швидкість
ν = πD n мм/хв, (2.3)
де D — діаметр, мм.
Якщо швидкість різання визначати в метрах за хвилину, то формулу швидкості треба поділити на 1000 і одержати швидкість різання фрезерування
(2.4)
Число обертів фрези за хвилину

ОБ/ХВ (2.5)
При фрезеруванні на величину швидкості різання впливають такі фактори: матеріал заготовки, різальні властивості фрези, діаметр і стійкість фрези, подача, глибина різання, ширина фрезерування, число зуб’ів фрези, охолодження та ін. При призначенні режимів фрезерування, залежно від конкретних умов, слід використовувати довідкову літературу.При обробці фрезеруванням подача заготовки може бути за напрямомпереміщення
оброблюваного виробу або подача на один зуб, подача за один оберт чи за хвилину. Тому за напрямом переміщення стола фрезерного верстата подачі бувають поздовжні, поперечні та вертикальні. При фрезеруванні розрізнюють подачу на один зуб, на один оберт і хвилинну.Якщо стіл фрезерного верстата здійснює поздовжнє переміщення, то і подача — поздовжня, відповідно при поперечному переміщенні подача буде поперечна, а при вертикальному —вертикальна.
Подача — це відстань, на яку переміщується оброблювана деталь за один оберт фрези, або на один зуб фрези, або переміщення деталі за одиницю часу (за 1 хв).Таким чином, подача при фрезеруванні може бути на зуб фрези Sz (мм/z), на оберт фрези So (мм/об) або хвилинна подача Sхв (мм/хв).
Подана на зуб — це величина переміщення стола із заготовкою або фрези при повороті на один зуб. Подана на один оберт фрези — це величина переміщення стола із заготовкою або фрези за один оберт фрези.Зв'язок між подачами на зуб і на один оберт виражається шляхом множення величини подачі на зуб на число зуб'їв фрези:
So = SzZ. (2.6)
Хвилинна подана — це величина відносного переміщення стола із заготовкою або фрези за одну хвилину.Хвилинну подачу визначають як добуток подачі на один оберт фрези та числа обертів фрези за хвилину:
SХВ = So n= SzZn, мм/хв. (2.7)
Для визначення необхідного часу для фрезерування поверхні деталі треба довжину обробки L поділити на хвилинну подачу:
To = L/Sхв (2.8)
З формули робимо висновок, що хвилинна подача характеризує продуктивність обробки.На величину подачі при чорновому фрезеруванні впливають такі фактори: матеріал заготовки, матеріал різальної частини фрези, потужність верстата, кути заточки фрези тощо, а при чистовому — шорсткість оброблюваної поверхні. Чорнове фрезерування виконують з найбільшими подачами. Наприклад, для фрезерування конструкційної сталі циліндричною фрезою зі швидкорізальної сталі при глибині фрезерування
t = 3...5 мм і ширині
В до 50 мм подача може бути 0,2...0,3 мм/зуб, а для чавуну — 0,10...0,12 мм/зуб. При фрезеруванні товщина стружки змінюється від найменшого значення
атіп до найбільшого a
max, тому переріз стружки й потужність фрезерування змінюються між мінімальним і максимальним значеннями.Швидкість різання, глибина різання і подача визначають режим різання.
Вибір раціональних режимів фрезерування
Під режимом різання розуміють сукупність параметрів різання, що забезпечують нормальну роботу верстатів за встановленим технологічним процесом. Раціональний (оптимальний) режим — це той, за якого сукупність параметрів дає найкращі результати. Інколи режим ще називають і так, як називають основний параметр.Режими різання при обробці металів знаходяться у взаємозалежності зі швидкістю різання, геометричними параметрами різальної частини інструмента й іншими умовами.
Одним з елементів режиму різання є швидкість різання, яка значно впливає на продуктивність та собівартість обробки. Збільшення швидкості підвищує продуктивність та інтенсивність спрацювання інструмента, тобто внаслідок більшого виділення теплоти стійкість інструмента знижується. Враховуючи це, необхідно в кожному конкретному випадку вибирати оптимальний режим різання. На величину швидкості різання впливають різні фактори (якість матеріалу, що обробляється, матеріал різальної частини інструмента, стійкість інструмента, подача та глибина різання, геометричні елементи різальної частини інструмента, вид обробки, охолодження тощо). Першорядне, вирішальне значення має стійкість інструмента — його різальні властивості.
Розглянуті вище елементи різання — глибина, подача та швидкість — визначають режим різання. Суть призначення режимів різання зводиться до встановлення найвигіднішого сполучення цих елементів. Правильно налагодженим для певних умов обробки буде той верстат, який забезпечує найпродуктивніше різання, високу точність і потрібну шорсткість оброблюваних поверхонь і економічність процеcу, тобто створює оптимальний режим різання. Оптимальним режимом називається така глибина різання, подача та швидкість різання, за яких процес обробки деталі буде най продуктивнішим та най економічним. Під економічністю розуміємо зниження собівартості обробки, витрати різального інструменту, покращення використання обладнання — робота з мінімальною затратою машинного та допоміжного часу. Призначити оптимальний режим для певних умов фрезерування виробу із заданого матеріалу, розмірів, форми тощо значить вибрати тип, розміри, матеріал і геометричні параметри різальної частини фрези та раціональні елементи режиму різання, умови охолодження й ін. Після цього треба встановити оптимальне значення елементів: B, L, Sz, ν, n, Nn, T.
Режим різання впливає на продуктивність праці. Вибір режиму залежить від потрібної швидкості та глибини різання, за яких досягається максимальна продуктивність. Для економічно вигідного процесу; треба вибирати найкращу комбінацію взаємопов'язаних і взаємозалежних елементів режиму різання. Зі зміною однієї з величин необхідно ї змінювати іншу, щоб не поламався інструмент та не виникло вібрування. Якщо за один робочий хід припуск на обробку h не вдається зрізати повністю, то визначають число робочих ходів за формулою i = h/t, де h — припуск на обробку, мм; t— глибина різання, мм.
Вибраний режим має забезпечити точність розмірів і потрібну шорсткість поверхні оброблюваної деталі, максимально можливу продуктивність праці, найменшу собівартість обробки, повне використання фрезерного верстата і різальних можливостей фрези.
Продуктивність праці при фрезеруванні залежно від обсягу знятого металу визначається за формулою

Після перетворення формули шляхом заміни n -го значення одержуємо
(2.9)
Проаналізувавши формулу, можна зробити висновки, що на продуктивність Q, мм3/хв, при сталому діаметрі фрези всі параметри фрезерування впливають однаково, бо кожен із них у формулі — в першому степені. Це означає, що при збільшенні будь-якого з них, наприклад удвічі (за інших сталих параметрів), продуктивність також збільшиться вдвічі. Параметри: B, t, Sz, Z і ν, впливають на стійкість фрези по-різному, тому, враховуючи цю обставину, слід вибирати допустимі параметри, які менше впливають на стійкість інструмента, наприклад: глибину різання, подачу на один зуб, швидкість різання. Швидкість різання максимально впливає на стійкість інструмента, тому її вибирають виходячи зі встановленої норми стійкості інструмента.
При фрезеруванні параметри режимів різання вибирають у такій послідовності:
вибирають фрези для обробки з необхідними для фрезерування показниками, тобто її діаметр, кількість зуб’їв, їх геометричні параметри, матеріал різальної частини;
визначають глибину різання;
визначають подачу;
визначають період стійкості фрези при фрезеруванні;
визначають швидкість різання;
визначають частоту обертання шпинделя верстата;
визначають необхідну потужність для фрезерування;
визначають машинний час.
Залежно від процесу обробки заготовки фрезеруванням із досвіду вибирають фрезу відповідної характеристики, щоб при фрезеруванні можна було раціонально використати продуктивність верстата та різальні властивості фрези. Визначення характеристики фрези має бути оптимальним з точки зору продуктивності та економічності використання верстата та інструмента. Оптимальність збігу потужності верстата та різальних властивостей фрези можуть зберігатися або бути близькими один до одного.
Можливі також випадки, коли виробничі можливості верстата не достатні й не можна повністю використати різальні властивості фрези і, навпаки, виробничі можливості верстата перевищують різальні властивості інструмента. На заводах є нормативні залежності, за якими лише одна залежність відповідає виробничим можливостям верстата і фрези, тобто має місце повне використання різальних властивостей інструмента та виробничих можливостей верстата. Бажано цю залежність призначити при виборі характеристики фрези.
Глибину різання фрезеруванням вибирають залежно від припуску на обробку; призначеної шорсткості поверхні деталі; потужності верстата та можливостей різального інструменту. Бажано припуск зняти за один прохід, але це не завжди можливо. Так, при чорновій обробці вибирають глибину різання t, що відповідає припуску і. Припуск знімають за один прохід при чорновій обробці з класом шорсткості поверхні від першого до третього. Якщо є потреба одержати четвертий — шостий класи шорсткості при так званій напівчистовій обробці швидкорізальною фрезою, глибину різання призначають у два проходи. Глибина різання першого проходу (чорнового) t = 3/4/, тоді другий прохід t = 1/4/. Глибина різання чистового фрезерування t= 0,5...1,0 мм. Якщо застосовують швидкісне фрезерування, то за один прохід можна одержати шорсткість поверхні від шостого до восьмого класу шорсткості.
Встановлюють величину подачі на зуб S
zпри чорновій обробці залежно від потужності верстата, міцності зуба фрези, міцності фрези (кінцеві та фрези невеликих діаметрів), міцності оправки фрези, пристрою та деталі, яка обробляється, жорсткості та вібростійкості верстата тощо. При чистовій обробці величина подачі має відповідати вимогам точності та шорсткості поверхні. Для визначення величини подач виконують розрахунки або використовують таблиці, де залежно від режимів різання наведені величини подач залежно від глибини різання, міцності заготовки тощо (табл. 2.1).
Таблиця 2.1 Режими різання при фрезеруванні сталі торцевою фрезою
Головнийкут у плані
| Глибина різання t,мм
| Межа міцності сталі σм Н/мм2
|
до 60
| 61...80
| 81..100
| 101...120
|
Подача на один зуб фрези S3, мм
|
| 1...12
| 0,24...0,35
| 0,16...0,24
| 0,12...0,18
| 0,09...0,14
|
| 1...8
| 0,28...0,42
| 0,19...0,28
| 0,15...0,22
| 0,12...0,18
|
| 1...5
| 0,40...0,60
| 0,28...0,42
| 0,21...0,32
| 0,17...0,25
|
При чорновому фрезеруванні сталі циліндричними фрезами зі вставними ножами беруть подачу на один зуб в межах 0,1...0,4 мм/зуб, для чавуну — подачу до 0,5 мм/зуб, а при чистовій обробці сталі й чавуну призначають подачу на один зуб фрези в межах 0,05...0,12 мм/зуб.
Період стійкості фрези при фрезеруванні визначають залежно від типу і розмірів фрези, умов процесу обробки, характеристики поверхні, що обробляється, та інших показників. При стійкості фрези Tхв слід ураховувати режим фрезерування, якщо ж застосовувати швидкісний режим роботи, то за довідковими даними треба вибрати відповідну стійкість. Залежно від призначеної глибини різання та подачі, відповідно їх величин, за стійкістю фрези визначають максимально допустиму швидкість різання, а за формулою або за таблицями нормативів — режими фрезерування. Призначені режими різання мають забезпечити: якість деталі за точністю та шорсткістю поверхні, максимальну продуктивність, найменшу вартість, раціональне використання верстата та інструменту. Для задоволення найкращих умов щодо режиму — після визначення нормативної швидкості різання розраховуємо оберти шпинделя за формулою

а потім за паспортом верстата підбираємо найближче число обертів шпинделя та визначаємо фактичну швидкість різання. Потім визначаємо ефективну потужність різання Nе за формулою або довідковими даними. Одержані результати порівнюємо з потужністю верстата. Треба, щоб Nе< Nв, якщо Nе> Nв, то необхідно призначити меншу швидкість різання, щоб задовольнити вимогам недостатньої потужності за формулою
(2.10)
де νN— швидкість різання верстата, м/хв; νт — швидкість різання за нормативами режиму різання, м/хв; Nе — ефективна потужність різання, кВт; N в — ефективна потужність верстата, кВт. Залежно від призначеної
(2.11)
швидкості різання ν
т ν
N вибирають найближчу частоту обертів шпинделя, а також визначають та підбирають найближчу подачу, що має верстат. Залежно від призначеної швидкості різання ν
т чи ν
N вибирають найближчу частоту обертів шпинделя, а також визначають та підбирають найближчу подачу, що має верстат. Машинний час на фрезерування визначається за формулою де
L — довжина переміщення інструменту або заготовки (з урахуванням врізування та перебігу), мм; S
хв — хвилинна подача, мм/хв. Для визначення параметрів режиму різання фрезеруванням використовують
номограми — спеціальні графіки, за допомогою яких визначають окремі параметри режиму різання фрезерування. Номограми для визначення частоти обертання фрези за швидкістю різання, діаметра фрези та хвилинної подачі за величиною подачі на зуб із заданим числом зуб’ів і частоти обертів фрези за хвилину наведено на рис. 2.5.
Графік номограми для визначення частоти обертання фрези за швидкістю різання (рис. 2.5,
а) використовують так: з точки, яка відповідає призначеній швидкості різання, проводять горизонтальну лінію, а з точки, що відповідає виробничому діаметру фрези, проводять вертикальну лінію. У точці перетину цих двох ліній буде вказана частота обертання фрези на верстаті. На графіку пунктиром вказані такі показники: швидкість різання 42 м/хв, діаметр фрези 110 мм, яка обертається при фрезеруванні за вказаних параметрів з частотою 125 об/хв.
Графік номограми для визначення хвилинної подачі за призначеною подачею на зуб із десятьма зуб'ями та частоти обертів фрези за хвилину (рис. 2.5, б) використовують так: з точки, що відповідає призначеній подачі на один зуб, проводять лінію, вертикальну до перетину похилої лінії на графіку, що відповідає числу зуб’ів фрези. З цієї точки проводимо горизонтальну лінію до перетину похилої лінії, що відповідає частоті обертання фрези. З цієї точки проводимо вертикальну лінію вниз до перетину показників хвилинної подачі. На графіку пунктиром вказані такі показники: подача на один зуб 0,2 мм/зуб, число зуб’ів фрези 10, частота оберту фрези 125 об/хв, хвилинна подача 250 мм/хв.
Поняття про поверхні деталей та їхня характеристика
Деталь — це з'єднання різних поверхонь: циліндричних, фасонних, плоских з пазами та виступами. До плоских належать поверхні, горизонтальність яких перевіряється ватерпасом. На плоских поверхнях можуть бути отвори, відкриті з трьох сторін, які називають пазами. Якщо над площиною зверху та з двох сторін виступають поверхні, їх називають виступами. До кожної деталі незалежно від розмірів і призначення ставляться такі основні вимоги: простота і довговічність, надійність у роботі, невисока вартість виготовлення та експлуатації. Одним із головних ефективних методів виготовлення деталей є принцип сумісності технологічних, економічних і організаційних завдань, які треба розв'язати під час побудови технологічного процесу обробки.
Основним напрямом скорочення витрат на виготовлення деталей машин вважається впровадження типізації технологічних процесів. Наприклад, обробка корпусних деталей залежить від їх класу, яким і визначається призначення, маса, форма з характерними поверхнями й відповідно ефективними методами технологічних процесів типових деталей машин.
Плоскі поверхні можуть бути горизонтальними, розміщеними під кутом, утворені з'єднанням кількох поверхонь з різноманітними пазами, виступами. Найбільш поширені деталі з плоскими поверхнями станини, які належать до корпусних деталей.
Корпусні деталі — це базові елементи виробу, тому технічні умови на їх виготовлення визначаються призначенням. Корпуси є важливими елементами машин.
До них належать коробки швидкостей і подач металорізальних верстатів, коробки передач транспортних машин, блоки циліндрів двигунів і компресорів, корпуси циліндричних, конічних, черв'ячних і комбінованих редукторів, насосів, плит тощо. Особливістю корпусних деталей є наявність у них плоских поверхонь — монтажних баз та отворів під опори. Тому до виготовлення корпусів ставляться високі вимоги щодо точності та шорсткості, бо від цього залежить загальна точність виробу. Базуванням за площиною та двома отворами забезпечується точність сьомого квалітета. Обробка корпусних деталей має забезпечити:
паралельність або перпендикулярність осей основних отворів;
співвісність отворів для упирання валів;
задані міжосьові відстані;
правильність геометричної форми отворів;
перпендикулярність торцевих поверхонь; осям отворів;
прямолінійність плоских поверхонь.
Заготовки корпусних деталей — звичайні виливки (чавунні або стальні) чи зварні. Під час конструювання заготовок необхідно виконати ряд вимог, які ставляться до них, — товщина стінок різних перерізів не повинна мати різких переходів і має враховувати всі вимоги формування. Під час виготовлення корпусу коробки передач технологічний процес обробки складається з обробки базових плоских поверхонь і отворів, обробки основних отворів, кріпильних та ін. Технологічний процес складається з різних операцій, наприклад чорнових та чистових. Зміст технологічного маршруту, обробки корпусів та застосування обладнання визначаються видом виробництва. Якість обробки плоских поверхонь визначають прямолінійністю в горизонтальних напрямах, паралельністю поверхонь між собою, необхідним нахилом однієї поверхні відносно іншої, точністю розмірів, шорсткістю та якістю за показниками технічних умов, необхідних для виготовлення та експлуатації. Плоскі поверхні обробляються струганням, довбанням, фрезеруванням, протягуванням і шліфуванням, а в одиничному виробництві для остаточної обробки площин інколи застосовують шабрування. Типові технологічні процеси обробки плоских поверхонь і пазів залежать від культури конструкційних розробок і масштабу виробництва. Обробку отворів і контроль оброблених поверхонь корпусних деталей здійснюють за розглянутими вище методами.
Рис 2.5 (а) Графік номограми для визначення частоти обертання фрези за швидкістю різання
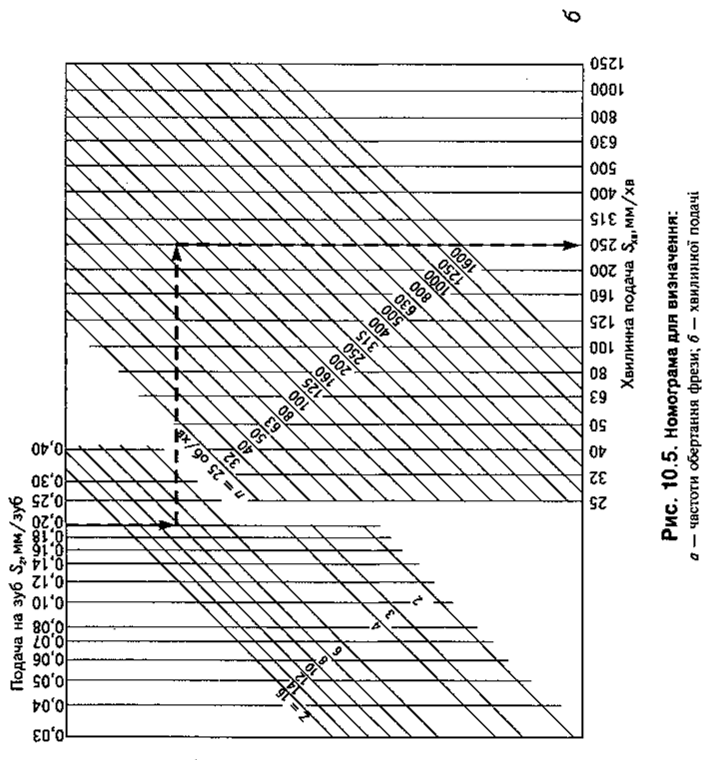
Рис. 2.5, (б) Графік номограми для визначення хвилинної подачі
Фрезерування плоских поверхонь
Обробку плоских поверхонь заготовок за допомогою різальних інструментів циліндричної форми з розміщеними по колу або торцю зуб'ями називають фрезеруванням. Розрізняють два види фрезерування: проти подачі, коли заготовка переміщується в напрямі протилежному обертанню фрези, і за подачі — заготовка рухається в напрямі обертання фрези. Різання та утворення стружки фрезою відрізняється від роботи різця або свердла. Різець і свердло протягом усього періоду різання перебувають у безперервному контакті з металом. У процесі фрезерування зуб'я фрези
працюють періодично на невеликій її частині. Зуб за кожний оберт фрези знімає із заготовки стружку, переріз якої змінюється, внаслідок чого створюється нерівномірність фрезерування, що впливає на сили різання, крутильного моменту та потужності. Фрезерування відзначається високою продуктивністю внаслідок участі у різанні великої кількості зуб’ів, що працюють у більш сприятливих умовах, ніж леза інших інструментів. Фрезерування здійснюється на фрезерних верстатах різних конструкцій, основними з яких є горизонтально - та вертикально-фрезерні. Зуб'я фрези в процесі фрезерування знімають стружку у вигляді коми. Фрезерування проти подачі поступово збільшує товщину стружки, а за подачею — зменшує. Фрезерування проти подачі підвищує продуктивність верстата внаслідок плавного збільшення об'єму стружки з поступовим врізуванням зуб’ів у метал під кіркою, що має перевагу порівняно з фрезеруванням за подачею. Недоліком фрезерування проти подачі є відривання заготовки від стола фрезою в процесі переміщення її проти руху подачі. Фрезерування кінцевими фрезами застосовують для обробки відкритих пазів різних виїмок, уступів, взаємно перпендикулярних площин, для фрезерування криволінійних контурів тощо.
Фрезерування торцевими фрезами застосовують для обробки плоских поверхонь, розміщених під прямим кутом до осі фрези, що лежать в одній або кількох площинах. Кінцеві та торцеві фрези призначені в основному для роботи на вертикально та горизонтально-фрезерних верстатах, а також можуть використовуватися і на копіювально-фрезерних, агрегатних верстатах з ЧПК. Застосування вказаних фрез для наведених виді обробки забезпечує підвищену продуктивність і точність. Обробка деталей зі складними поверхнями, наприклад профілю лопастей турбін, фрезами з гвинтовими зуб'ями забезпечує кращі умови різання та відведення стружки. Обробка фрезами з гвинтови ми зуб'ями порівняно з прямозубими фрезами забезпечує підвищення режимів різання (швидкості, подачі) на 30...50 %. Гвинтовий зуб фрези врізується в метал плавніше без вібрування, внаслідок чого можна збільшити подачу та поліпшити якість обробки й довговічність фрезерного верстата. Під час фрезерування фрезою з гвинтовим зубом ширина шару, що зрізується протягом робочого циклу зростає (фрезерування проти подачі) від нуля до максимального, потім спадає до нуля, коли припиняється контакт різальної кромки і поверхнею різання. Врахувавши, що в контакт з поверхнею вступають кілька різальних зуб’ів, які або тільки починають роботу, або закінчують її, можна підібрати такі параметри, коли сумарна товщина шару, що зрізується, буде сталою, тобто забезпечити рівномірність фрезерування.
Для виконання будь-яких робіт на фрезерному верстаті треб дотримуватися таких підготовчих процесів:
підібрати фрезу та заготовки і закріпити їх відповідним чином;
згідно вибраному процесу обробки виставити заготовку відносно фрези, переміщуючи стіл верстата для фрезерування;
налагодити верстат для фрезерування — зробити необхідні розрахунки для призначення режиму різання — визначити глибину різання, подачу, швидкість різання для встановлення частот ти обертання шпинделя.
Закріплення заготовок і фрез, їх встановлення на верстаті потребує двох видів пристроїв, які були вже розглянуті вище. Проте слід зауважити, що закріплення буде виконуватися залежно від розмірів, конструкції та процесу фрезерування, чим керуються при підготовці до роботи. Крім того, заготовка і фреза повинні точно займати необхідне положення, бо це визначає точність форми і розміщення поверхонь деталей, що фрезерують. Якість оброблених площин можна визначити за такими показниками:
· збіжністю дійсних розмірів деталі та розмірів креслення, тобто точністю;
· похибки різних відхилень точності мають бути в межах допуску на неточність виготовлення за прямолінійністю та площинністю;
· відхилення від паралельності, перпендикулярності, нахилу, симетричності розміщення окремих граней деталі відносно інших мають відповідати встановленим допускам.
Розрізняють фрезерування площин грубе, чорнове, напівчистове й чистове. Залежно від припуску обробки та глибини різання буде відповідний вид фрезерування, наприклад, обробка з нерівномірним припуском понад 8 мм і обробка по кірці називається грубою; обробка з глибиною різання 3...8 мм без кірки з відносно рівномірним припуском називається чорновою; обробка з глибиною різання 1,5...3,0 мм з рівномірним припуском і шорсткістю обробленої поверхні Rz= 40 мкм називається напівчистовою; обробка площин з глибиною різання до 1,5 мм з рівномірним припуском і шорсткістю обробленої поверхні до R а = 2,5 мкм називається чистовою обробкою.
Фрезерування циліндричними фрезами
Фрезерування площин циліндричними фрезами — найпоширеніший вид обробки на горизонтально-фрезерних верстатах. Фрезерування площин виконують і на вертикально-фрезерних верстатах із застосуванням торцевих фрез. Циліндричні фрези бувають суцільні та збірні зі вставними ножами Вставні ножі (зуб'я) виготовляють із швидкорізальної сталі або з твердого сплаву. Суцільні фрези виготовляють з дрібними і крупними зуб'ями зі швидкорізальної сталі. Застосування фрез із вставними ножами економічно вигідно, бо зменшується витрата коштовного інструментального матеріалу. При чорновому і напівчистовому фрезеруванні застосовують фрези з крупними зуб'ями. При чистовому і напівчистовому фрезеруванні застосовують фрези з дрібними зуб'ями. Залежно від конкретних умов обробки деталей фрезеруванням вибирають тип, розмір фрези, враховуючи матеріал, марку, розміри заготовки, величину припуску на обробку тощо.
На заводах використовують спеціальні номограми для практичного вибору оптимальних розмірів суцільних циліндричних фрез з різними зуб'ями (дрібними і крупними) з урахуванням характеристики матеріалу заготовки, що обробляється. Номограму для вибору суцільних циліндричних фрез наведено на рис. 2.6. Основні розміри циліндричних фрез такі: довжина фрези
L, діаметр фрези
D діаметр отвору
d, кількість зуб’ів z, ширина фрезерування
В. Матеріали умовно позначені так: важкооброблювані (наприклад, сталь некорозійна, жароміцна) Т, середньої трудності обробки (наприклад, конструкційна сталь, чавун сірий) С, легкооброблювані (наприклад, мідь та її сплави, алюміній і його сплави) Л, І — чорнова обробка, II — чистова обробка. Визначення основних розмірів циліндричних фрез на графіку номограми показано штриховою лінією зі стрілками. Визначимо всі розміри фрези, користуючись номограмою (див. рис. 2.6). Згідно графіка номограми ширина фрезерування
В дорівнює 75 мм. За шириною визначаємо довжину фрези
І. Значення ширини фрезерування визначаємо за вертикальною стрілкою. Стандартне значення довжини фрези в даному разі дорівнює 80 мм. Далі визначаємо діаметр посадочного отвору фрези (або діаметр оправки). Для цього із точки, яка відповідає
L = 80 мм, проводимо вверх вертикальну пунктирну лінію до перетину її з похилою лінією С-І, яка відповідає умовам оброблюваного матеріалу (чорнова обробка металу середньої трудності). З точки перетину двох ліній проводимо горизонтально пунктирну лінію до перетину з віссю посадочного отвору фрези
d (діаметр) оправки. За графіком номограми точка перетину визначає приблизно
d = 40 мм, тому вибираємо фрезу з діаметром 40 мм.
Далі знаходимо діаметр фрези D. Для цього із точки перетину d = 40 мм продовжимо пунктирну лінію горизонтально до перетину з похилою лінією І (чорнова обробка). З цієї точки проводимо пунктирну вертикальну лінію вниз до перетину з віссю В (діаметр фрези). За графіком номограми діаметр фрези D приблизно дорівнює 100 мм. Далі продовжуємо проведення вертикальної лінії вниз до перетину її з похилою лінією С-І, яка відповідає умовам обробки. З точки перетину цих двох ліній проводимо пунктирну горизонтальну лінію до перетину з віссю z (кількість зуб’ів фрези). Точка перетину знаходиться між z = 12 і z = 14. Вибираємо z=12 зуб’ів, бо z= 14 зуб’ів за стандартом немає. Використовуючи номограму, визначаємо параметри суцільної циліндричної фрези з крупними зуб'ями: L = 80 мм, D = 100 мм, d = 40 мм, z=12. Далі, використовуючи довідник технолога, визначаємо оптимальні геометричні параметри фрези: γ =15°, d =5°. Крім наведеної номограми, є й інші, за якими можна визначити основні розміри циліндричних фрез із вставними ножами тощо. Циліндричні фрези поділяються на право - і ліворізальні. Розрізняють їх залежно від напряму обертання фрези при фрезеруванні. Праворізальними називають фрези, які під час фрезерування обертаються за годинниковою стрілкою, якщо процес роботи спостерігати з боку заднього кінця шпинделя (або проти годинникової стрілки, якщо спостереження вести з боку підвіски — серги).

РИС. 2.6. Номограма для вибору розмірів суцільних циліндричних фрез
Ліворізальними називають фрези, які під час фрезерування обертаються проти годинникової стрілки, якщо процес роботи спостерігати з боку заднього кінця шпинделя (або за годинниковою стрілкою, як спостереження вести з боку підвіски — серги).Праворізальна фреза відкидає стружку праворуч, а ліворізальна — ліворуч, якщо спостерігати за роботою фрези з боку підвіски — серги. Залежно від встановлення фрези на оправці її можна використовувати і як праворізальну, і як ліворізальна.
Таким чином, залежно від потреби напрям різання можна змінювати, повертаючи фрезу на оправці. Звичайно на виробництві для фрезерування на горизонтально-фрезерному верстаті застосовую фрези з лівим напрямом гвинтових канавок для обертання шпинделя верстата з правим напрямом і навпаки, фрези з правим напрямок гвинтових канавок застосовують для обертання шпинделя верстата лівим напрямом.

Рис. 2.7. Закрыплення фрез ыз спыральними зб’ями
а – правельне; б – неправельне
Такий взаємозв'язок напряму гвинтових канаво фрези та її обертання в різні напрями спричинюється дією осьової сили
Рх бо у цьому разі вона спрямована в бік шпинделя. У разі, коли напрями гвинтових канавок фрези і її обертання збігаються, осьова сила
Рх витягує фрезу з оправкою з конусного отвору шпинделя і тисне на підвіску — сергу. Жорсткість опор шпинделя і підвіски — серги різні. Жорсткішою опорою є шпиндель, тому при обробці фрезеруванням слід вибирати різні напрями гвинтових канавок фрезі обертання. Якщо при фрезеруванні осьова сила
Рх спрямована в протилежний бік шпинделя, то фрезу треба зняти з оправки і повернути її іншим торцем, тобто треба встановлювати фрези з гвинтовими канавками так, щоб сила
Рх притискувала оправку до шпинделя верстата (рис. 2.7). При встановленні фрезу необхідно розмістити поближче до станини і перевірити її обертання на биття.

Рис. 2.8. Перевірка биття фрези індикатором.
Перевіряють биття фрези за допомогою рейсмуса або індикатора. Перевірку індикатором за величиною відхилень стрілки індуктора показано на рис. 2.8. Для перевірки індуктор треба закріпити на штативі та встановити на столі верстата, підвести стрілку індикатора до фрези, як показано на рис. 2.8. Для фрезерування площин заготовки закріплюють на столі верстата прихватами, притискачами, упорами на кутових плитах або в машинних лещатах. Процес установлення заготовок для обробки на фрезерних верстатах було розглянуто вище. Режими різання фрезеруванням для циліндричної фрези визначають за формулами, розглянутими вище для швидкості різання, подач і глибини різання, які залежать від припуску. Припуск на фрезерування площин циліндричними фрезами залежить від виду обробки та матеріалу заготовки. Величина припуску на обробку заготовок дорівнює 0,1...0,6 мм, а величина подачі становить 0,05...0,30 мм/зуб. Розмір подачі залежить від матеріалу різальної частини фрези та матеріалу, що обробляється. При фрезеруванні фрезами зі швидкорізальної сталі швидкість різання досягає 25...60 м/хв, і 80...300 м/хв — при фрезеруванні твердосплавними фрезами. Режими різання фрезеруванням площин циліндричною фрезою з діаметром
D - 75... 100 мм, з глибиною різання
t=6 мм, а також величини швидкості різання та подача наведені у табл. 2.2. При використанні режимів різання рекомендуємо вибирати для чистового фрезерування більші значення швидкості різання і менші — подачі. У разі вибору більшої подачі, слід вибирати меншу швидкість різання. При обробці стальних заготовок швидкорізальною фрезою застосовують охолодження емульсією.
Таблиця 2.2 Режими різання для циліндричної фрези
Матеріал фрези
| Сталь σм = 75 Н/мм2
| Чавун НВ 190
|
Швидкість, м/хв
| Подача, мм/зуб
| Швидкість, м/хв
| Подача, мм/об
|
Швидкорізальна сталь
| 25…50
| 0,05…0,3
| 25…35
| 0,1…0,4
|
Твердосплавна сталь
| 120…300
| 0,05…
| 60…120
| 0,1…0,2
|
При чорновому фрезеруванні знімається припуск за один прохід, тобто глибина різання дорівнює припуску. Чистове фрезерування виконують за два проходи. Величина припуску першого проходу дорівнює 3/4 припуску, а другого — 1/4 припуску. Таким чином, чорнова глибина різання — 3/4 припуску, чистова — 1/4 припуску. Для налагоджування верстата та встановлення подачі на потрібну величину використовують лімб.
Фрезерування торцевими фрезами
Фрезерування плоских поверхонь торцевими фрезами виконується на вертикально і горизонтально-фрезерних верстатах. Найчастіше фрезерують площини торцевими фрезами на вертикально-фрезерних верстатах. Якщо порівнювати торцеві фрези з циліндричними, то перші мають такі переваги: жорсткіше кріплення, плавніший рух, одночасно працює велика кількість зуб’ів. У торцевих фрез зуб'я розміщуються на циліндричній поверхні й на торці. Торцеві фрези можуть бути суцільними з конусним хвостовиком і насадними з дрібними і крупними зуб'ями та зі вставними ножами. Торцеві фрези із пластинами твердих сплавів застосовуються значно ширше за інші, бо фрезерування ними є продуктивнішим, ніж обробка деталей циліндричними фрезами. Торцеві фрези мають головні та допоміжні різальні кромки, розміщені на робочій поверхні. Головними називають частину, розміщену на циліндричній поверхні, а допоміжними — на торцевій поверхні.
Торцеві фрези поділяють на право - та ліворізальні. Праворізальними називають фрези, які під час роботи обертаються за годинниковою стрілкою, а ліворізальними — ті, які обертаються проти годинникової стрілки (якщо дивитися на фрезу або фрезерну головку зверху). Основні розміри торцевих фрез, як і циліндричних, такі: діаметр D довжина L, діаметр посадочного отвору d і кількість зуб’ів z. У торцевих фрез величини основних розмірів взаємозв'язані таким чином, що кожному діаметру D відповідає певна величина розміру довжини L фрези, діаметр отвору d і кількість зуб’ів z. Налагодження вертикально і горизонтально-фрезерних верстатів із торцевими фрезами принципово не відрізняється від налагодження горизонтально-фрезерного верстата з циліндричними фрезами. Торцеві насадні фрези закріплюють на верстаті за допомогою оправок, які мають конічний хвостик, що вставляється в шпиндель верстата.
Далі виконують процеси на вертикально-фрезерному верстаті так само, як і на горизонтально-фрезерному: перевіряють напрям і обертання фрези та її биття, встановлюють і закріплюють заготовку на столі; вибирають режим різання для фрезерування площин. Значення швидкості різання і подачі при глибині різання 6 мм, що рівнозначно умовам фрезерування циліндричною фрезою, діаметр якої 75 мм, наведено у табл. 2.3.
Діаметр торцевої фрези, залежно від ширини фрезерування,
D = (1,3...1,8)В
і вибирають його залежно від ширини стола верстата:
Ширина стола, мм 160 250 320 400
Діаметр фрези, мм 50...100 80...160 100...200 125...250 Для вибору мінімального діаметра фрези можна використати залежність
В = (0,6...0,8)В.
Таблиця 2.3 Режими різання для торцевих фре з
Матеріал фрези
| Сталь σм = 75 Н/мм2
| Чавун НВ 190
|
Швидкість, м/хв
| Подача, мм/зуб
| Швидкість, м/хв
| Подача, мм/об
|
Швидкорізальна сталь
| 30...55
| 0,03...0,3
| —
| —
|
Твердосплавна сталь
| 200...300
| 0,06...0,2
| 60...100
| 0,2...0,6
|
Технологія фрезерування площин торцевою фрезою на вертикально-фрезерному верстаті майже не відрізняється від фрезеруваня ня на горизонтально-фрезерному верстаті циліндричною фрезою Проте при обробці заготовок за однакових умов роботи торцева фреза працює плавніше і обробка поверхні буде якіснішою, ніж при роботі циліндричною фрезою. Торцевими фрезами можна виконувати чорнову та чистову обробку площин. Для чорнової обробки рекомендується застосовувати торцеві насадні фрези із вставними ножами або з крупними зуб'ями, а при чистовій краще фрезерувати торцевими насадними фрезами з дрібними зуб'ями.Кращими для фрезерування є торцеві фрези з різальними елементами із твердих сплавів. Для фрезерування торцевими фрезами горизонтальних площин заготовки закріплюють так само, як і при обробці на горизонтально-фрезерних верстатах за допомогою прихватів, лещат та інших пристосувань.

Рис. 2.9. Фрезерування похилих плошин торцевою фрезою:
а – із застосуванням спеціального пристрою;
б – поворотом шпинделя накладної головки
На вертикально-фрезерних верстатах із застосуванням торцевих фрез можна фрезерувати похилі площини та скоси, встановлюючи оброблювані заготовки із застосуванням універсальних лещат, поворотних столів і спеціальних пристроїв (рис. 2.9, а) або поворотного шпинделя вертикально-фрезерного верстата (рис. 2.9, б). Таку обробку можна виконувати на вертикально-фрезерних верстатах з поворотними головками шпинделя та