1. Вариативность технологической среды - отношение времени всех вспомогательных движений, требующихся для обеспечения данного техпроцесса к суммарному времени всех движений, выполняемых в данном техпроцессе (движения инструмента, заготовки и устройств разного рода).
где Т – общее время всех движений, заложенных в техпроцессе; например, при автоматизации сборочной операции, как части техпроцесса, вместо человека устанавливается специальное сборочное устройство, которое должно обеспечить различные вспомогательные движения(взятие детали, ее перенос, наживление, завертывание).
Отсюда возникают 2 возможности автоматизации:
Поставить 1 сложное устройство, выполняющее все движения
Установить несколько простых устройств, обеспечивающих указанные движения по отдельности
Отсюда, в зависимости от времени выполнения этих движений будет зависеть и вариативность техпроцесса.
Противоположным свойством является - постоянство показателей техпроцесса, и это свойство определяется свойством детерминированность.
|
|
2. Вариативность движений, применяемых в техпроцессе- это отношение КТ - числа темпов движений, заложенных в техпроцессе к Ко – общему количеству типов движений.
3. Частота смены технологии ,
где wi – частота использования i – го техпроцесса в данном производстве, т.е. здесь используются количественные показатели различных типов движений, просуммированные для данных техпроцессов, а также изменяемость самих техпроцессов.
Источником вариативности техпроцессов можно считать:
1. Нестабильность свойств материала заготовки
2. Нестабильность поступаемого сырья
3. Нестабильность свойств режущей части инструмента
4. Непостоянство конструкции инструмента
Дополнительным источником нестабильности автоматизированного техпроцесса является потеря ориентации детали после обработки на станке (деталь должна в ориентированном виде поступать на следующий станок, тогда будет нужно меньше вспомогательных движений).
Для преодоления вариативности (нестабильности) техпроцессов создать организованные условия, исключающие вышеупомянутые отклонения. В случае сохранения нестабильности техпроцесса (непостоянство механических свойств материала и припуска на обработку) целесообразно использование адаптивного управления.
31 Адаптивное управление. Качество обработки как управляемый показатель техпроцесса. Этапы управления
Адаптивные системы управления – позволяют управлять объектом или процессом в зависимости от накопления текущей информации, поступающей в СУ, как об изменении управляемого параметра, так и информации об изменении внешних условий (Пример: непостоянство механических свойств заготовки по длине обрабатываемой детали)
|
|
Основной задачей технологии машиностроения является достижение качества деталей.
Точность обработки –совпадение реально полученной детали с неким геометрическим прототипом или это степень приближения к этому прототипу.
Это:
1. Точность расстояния между поверхностями (размер)
2. Точность отдельной поверхности (погрешность формы)
3. Точность относительного расположения поверхностей.
4. Волнистость и шероховатость
Обеспечение точности производится в несколько этапов:
1. Необходимо достичь начальную точность установкой детали относительно баз станка (6 точек).
2. Обеспечивает проверку положения деталей относительно баз станка, в частности, определяется расположение припуска на установленную деталь для этого используют специальные контрольные – мерительные щупы (см ниже). Эти данные вводятся в систему станка и служат для коррекции последующей обработки с использованием программы
Основными показателями при обработке деталей с использованием адаптивного управления является обеспечение стабильных данных по точности размеров, по величине деформации деталей на которые в первую очередь влияют усилия, возникающие при резании.
Учитывая вышесказанное, особо следует выделить важность применения специальных устройств “адаптивные приводы (головки)”. В первую очередь такие устройства применяют для легко деформируемых деталей (нежесткие валы l/d³10…12).
При реализации таких методов одним из способов управления является целенаправленное изменение одного из технологических режимов, связанных с образованием силы резания (подача, скорость резания реже).
Пример управления точностью обработки:
1.С помощью упругих перемещ-й элем-тов технол-кой системы (корректировкой размера статической и динамической настройки
|
|
|
|

|
|
|

|
|
|
|

|

|

|
|
|
|
|
|
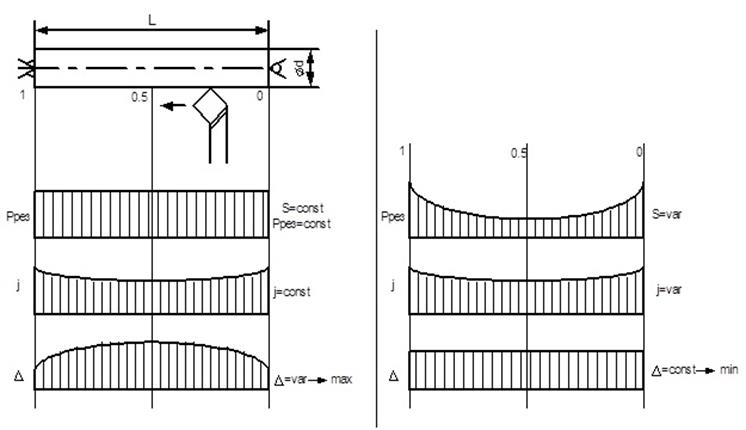
Рисунок 42 - Управление точностью обработки
При обработке таких деталей обычным методом под действием возникающей силы резания, деталь получает деформацию среза, в результате чего на готовой детали образуется погрешность “бочкообразность”, поэтому в данном примере идет управление режимами обраб (подачей) с таким расчетом, чтобы обесп-ть min погр-ть обраб и max точн-ть обраб.
Данный метод успешно реализуется по 2 направлениям:
1.С использованием вышеупомянутых специальных устройств
2.Мб исп-ван обычный станок с ЧПУ, где в программе заложено измен-е подачи по длине подачи в соотв с заданным значением.
Существует метод коррекции траектории дв-я вершинки резца путем создания ступенчатой траектории, заменяющей линию прогиба детали (метод периодических поднастроек резца).
Разработан также метод управления точностью упругими перемещениями, когда в качестве исполнительного механизма служит задний центр, он периодически по мере движения резца вдоль детали смещается на резец.
35 Контроль в системах управления технологией и оборудованием. Устройство и принцип действия контрольно-измерительного щупа. Примеры его применения
В настоящее время широкое применение находят специальные устройства “контрольно-измерительные” щупы.
Его назначение:
Измерение размеров деталей по окончании обработки
Измерение погрешностей формы деталей
Проведение промежуточного контроля в процессе обработки
Устройство предназначено для двух видов оборудования ЧПУ:
|
|
1. Контрольно-измерительные машины – в этом случае устройство устанавливается в шпинделе этой машины с помощью конического хвостовика
2. Обычный МРС типа “обрабатывающий центр” в этом случае устройство устанавливают по программе вместо инструмента.
Рисунок 47 – Контрольно-измерительный щуп
Устройство состоит из следующих элементов:
1. Корпус
2. Стандартный хвостовик
3. Измерительный стержень
4. Рабочий наконечник – шарик диаметром 3…4 мм, выполняемый из наиболее износостойких материалов (металлокерамика, искусственный рубин), для устранения загрязнений.
Рабочий наконечник постоянно обдувается воздухом через отверстие в корпусе.
5 – Датчики индуктивного типа, располагаются попарно под углом 900 друг от друга.
6 – Упругие механизмы возврата стержня в исходное положение.
При работе такого устройства выделяют три этапа:
1. когда по программе измерительный стержень подводится к детали “подвод” U = 0;
2. “касание поверхности детали”. Сопровождается появлением сигнала с датчиков, так как зазор между стержнем и соответствующим датчиком изменяется, в этот момент системой управления запоминается координата точки касания, необходимая для измерений;
3. “перебег” - вынужденное явление, так как мгновенная остановка узла невозможна.
Рисунок 48 – Этапы работы контрольно – измерительного щупа
Примеры использования данного устройства:
1 – Измерение диаметра расточенного отверстия.
Рисунок 49 - Схема измерения.
Диаметр шарика – постоянная величина.
Д = Lр.х. + dш = (Х3 – Х2) + dш (11)
Первая точка выбирается произвольно по координате “х”, но с условием, что она должна лежать в диаметральной плоскости отверстия. Точки 2 и 3 – точки касания с противоположными стенками отверстия, так же должны лежать в диаметральной плоскости отверстия.
2 – Измерение межцентрового расстояния для аналогичной детали.
Рис - Схема измерения.
Точки 1 и 2 выбираются на торце детали. Координаты точек 1 и 2 усредняются для исключения погрешности самой базовой поверхности. На поверхности отверстия определяются точки 3, 4, 5, расположенные под 1200 по отношению друг к другу. По координатам этих точек рассчитывают координату центра отверстия (точка 6), и она сравнивается с усреднённым значением координат точек 1 и 2.
|
|
3 – Измерение углов.
В этом случае на каждой поверхности берут по две точки, и по их координатам определяют направления поверхностей, образующих угол.
Рисунок 51 - Схема измерения угла
4 – Определение отклонения от плоскосности деталей типа плита.
Рисунок 52 - Схема измерения погрешности
Плита разбивается на части двумя диагоналями, на каждой из которых выбирают не менее пяти точек, причём, одна точка берётся в центре детали.
5 – Отклонение от цилиндричности.
Рисунок 53 - Схема измерения.
Согласно схеме измерение происходит за один оборот, при этом щупу сообщают движение подачи, а измеряемой детали – вращение вокруг оси.
37 Диагностика состояния технологической системы. Методы контроля величины износа инструмента для его автоматической смены.
Для обеспечения точности обработки нежестких деталей, а кроме того для сохранения материала режущей части инструмента были разработаны методы контроля состояния инструмента. В автоматизированном производстве возникает дополнительная задача принудительной замены инструмента по мере его износа, для этого в магазины станков устанавливают “инструменты дублеры”. Принудительно производится замена инструмента при окончании обработки одной детали.
Поэтому разработаны методы контроля:
1. По количеству обработанных данным резцом деталей, для этого на станке устанавливают счетчик обработанных деталей при этом мы исходим, что резец имеет постоянную и наперед известную стойкость. Однако это метод в настоящее время широко не применяется, так как имеется большой разброс по стоимости инструмента.
Недостатки метода:
Резец будет сниматься со станка не полностью выработав свой ресурс или будут встречаться поломки инструмента т.е. произойдет потеря материала режущей части
Кроме того возможен брак детали при поломке во время обработки
Работа резца в процессе обработки по следующей зависимости: когда износ резца идет с различной скоростью и при этом учитывается время обработки детали (или длина пути резания) по графику.
I – приработочный (начальный) износ. В автоматизированном производстве этот этап стараются исключить т.к. идет интенсивный износ ведущий к изменению размеров обрабатываемой детали. Для этого выполняют доводку резцов.
II – характеризуется равномерным и прямопропорциональным износом по отношению к времени работы t, который можно заранее учесть или спрогнозировать. Все методы основаны для этого участка.
III - катастрофический износ, заканчивающийся поломкой инструмента (неприемлем).
2. Контроль износа инструмента по величине тока нагрузки в цепи двигателя главного движения.
Метод основан на эффекте: изношенный инструмент ведет к возрастанию тока нагрузки. Метод реализуется так: в цепи питания двигателя установлен датчик тока нагрузки, по его показаниям судят о величине износа инструмента.
Рисунок 44 – Контроль износа инструмента по величине тока нагрузки в цепи двигателя главного движения
Работа новым инструментом характеризуется начальным значением тока IН по мере достижения допустимого значения [I] при износе инструмента (момент t1) следует указание о замене инструмента на его дублер. Если обработка продолжается этим инструментом то в момент t2 возможна поломка инструмента.
Преимуществом является простота метода, не требующая модернизации станка.
Недостатком - не высокая чувствительность метода, что позволяет применять его для черновой, грубой обработки.
3. Косвенный метод определения износа инструмента.
Контроль резца производится по величине фактического диаметра обработки с использованием сжатого воздуха, подаваемого через державку резца в направлении детали, причем давление воздуха строго стабилизировано. В цепь подачи воздуха установлено реле давления, срабатывающее на увеличение давления воздуха, отключая станок. Возрастание давления вызвано уменьшением зазора между резцом и деталью при износе резца.
Недостатком является то, что, контроль износа связан с возможным браком деталей т.к. диаметр Д детали непосредственно связан с зазором Z.
Рис - Косвенный метод определения износа инструмента
Известны и др. методы контроля, но они имеют ограниченное применение по сравнению с этими четырьмя.
4. Контроль состояние режущего инструмента по величине силы резания.
Метод является наиболее объективным и точным т.к. основан на измерении силы резания непосредственно. Для этого используют обычную схему включения тензодатчиков, размещенных таким образом: один из датчиков наклеивают на неподвижную часть резцедержателя (нижняя стенка паза), второй на верхней стенке паза и воспринимает деформацию верхней части резцедержателя под действием силы резания. Так как деформации резцедержателя по закону Гука прямопропорциональны действующей нагрузке (силе резания), то мы можем объективно судить и о величине износа. Деформации не велики и не превышают нескольких 0,01 мм.
Рис – Контроль состояния режущего инстр-та по силе резания
Датчик включается так что Д1 дает базовый сигнал U1=const, сигнал Д2 будет меняться в зависимости от силы резания, изменение которой при износе резца регистрируется через сопротивление R данного датчика.
где r - удельное сопротивление материала дат
l(Dl) – удлинение проводника под действием
S – площадь поперечного сечения проводника датчика;
DR – приращение сопротивления датчика.
39 Датчики, применяемые в системах управления, их
классификация и схемы основных устройств.
Датчики – особый вид устройств, которые в системах управления обработкой деталей служат двум целям:
1. Определение конечных положений различных узлов;
2. применяются в контрольно-измерительных устройствах, для определения фактических размеров обрабатываемых деталей.
Датчики по принципу действия подразделяют на:
1. Электроконтактные;
2. Виброконтактные;
3. Пневматические датчики (однопредельные, моногопредельные, дифференциальные);
4. Индуктивные датчики;
5. Пьезокерамические датчики;
6. Тензо-резисторные датчики (тензодатчики).
Примеры датчиков: